2021.01.01. ----5ページ目----- PAGE 1 2 3 4 5 6 7 8 9 10
よく製作家の工房内風景で、ロゼッタ部分だけ施したトップ板が何枚もぶら下がっている写真とか見た事ありませんか?
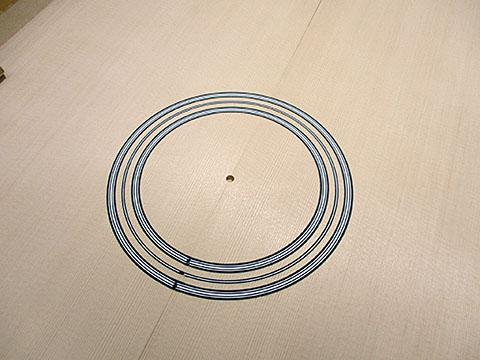
アコースティックギターの製作、トップ板の場合、まずこの段階まで仕上げてから次の作業(ブレイシング等)なので、「うちのロゼッタデザインはこれだよ」っていうブランドの"顔"があれば、ここまで施工してから何枚も吊して保管しておくのもごもっとも。
さあ、ここからは新しいトップ板に「ブレイシングの位置」を記していく作業です。
サウンドホールの中心位置が分かるようにレーザー加工機で、こんな透明アクリル板を作ってみました。パコッとはめれば中心がすぐ分かるので位置合わせに便利。。。。一度しか使わんけど
中心線を合わせて、新トップ板(裏面)の上に旧トップ板を載せる。マスキングテープで固定。
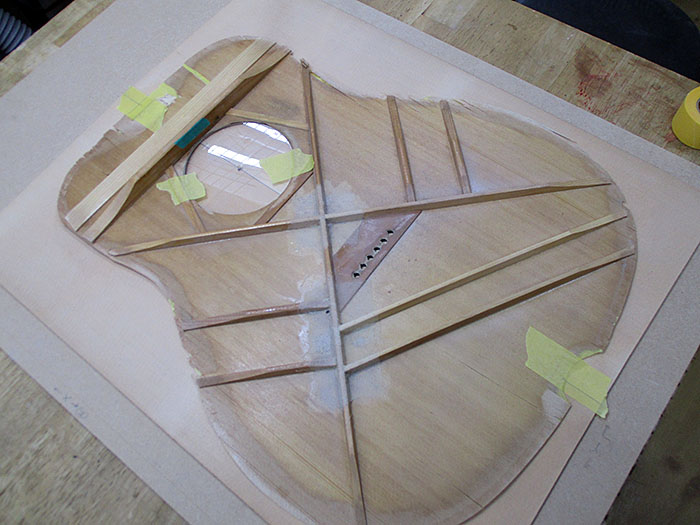
Xブレイシングの交差角度は90度(直角)でした。珍しい・・・・ で、↓↓こんな感じでブレイシングの位置を記していく。
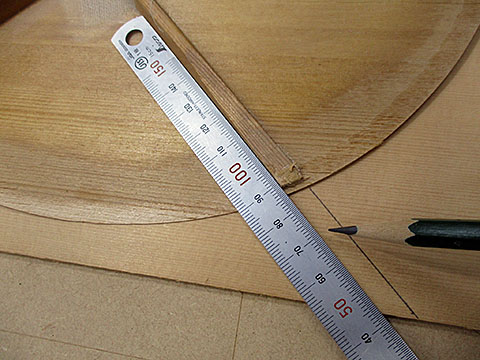
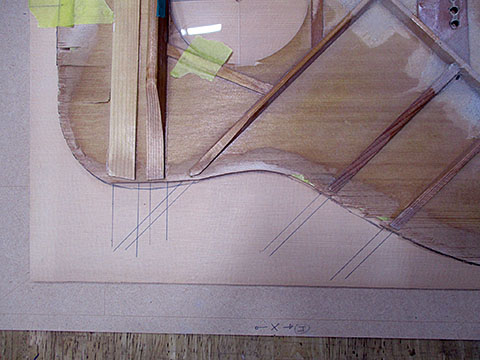
最後に外周も書きますが、旧トップ板はけっこうボロボロなので正確な外周線が分かりづらい。
そこで型から外したサイド&バックの本体を逆さまに当てがい、補足しました。
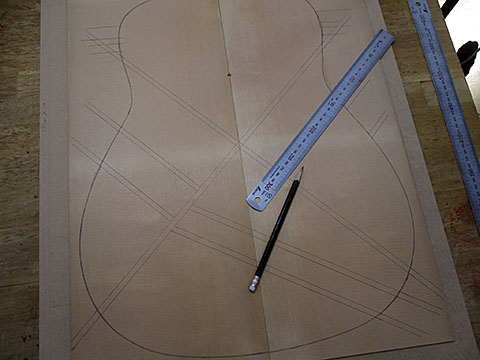
この段階で気づいたのですが、サウンドホールの直径は103mmが正解です。
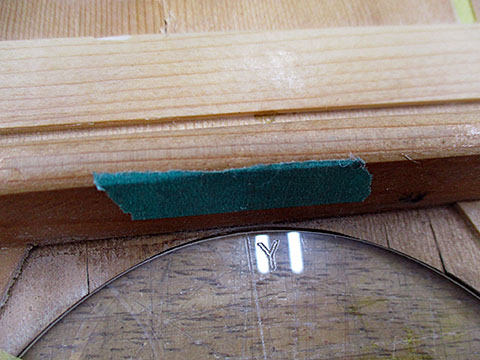
たぶんこういう事かと↓↓・・・・
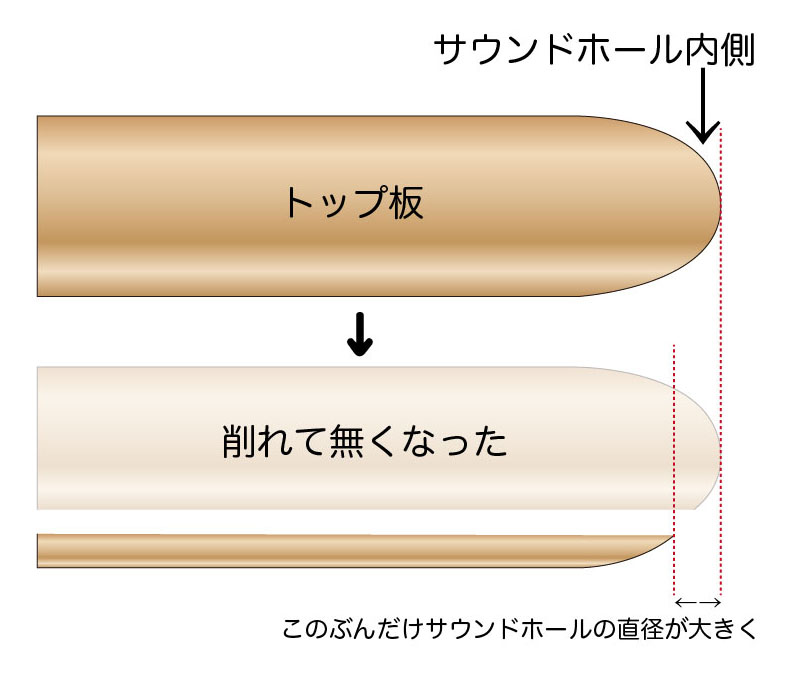
やけにトランスバースブレイスと近いな〜って思ってたんですよね。
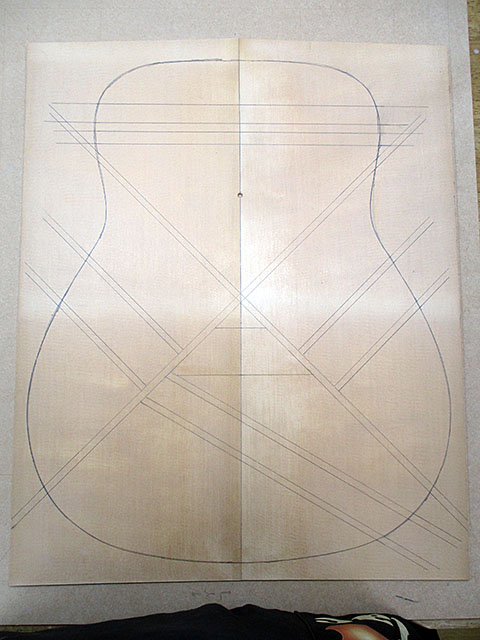
これで下書きは完成。
休憩
少し前の話しだが、8月から健康のために週に3〜4日、朝5時起きで4kmほどウォーキングをしている。
(冬は寒いのでもうやめた(笑))
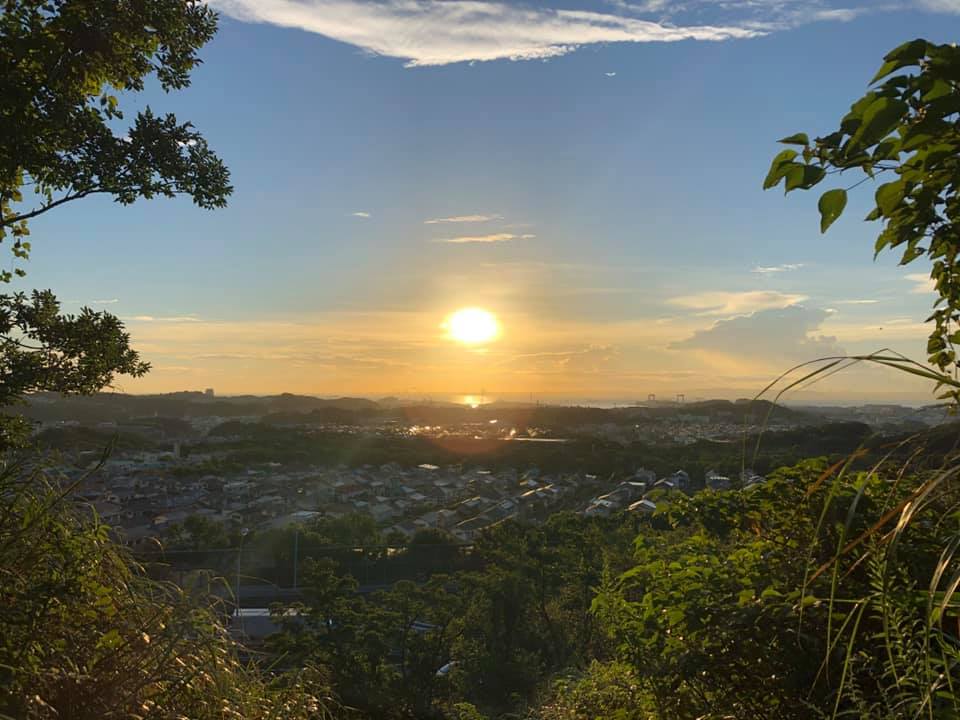
自宅から徒歩10〜15分で行ける、鎌倉へ続くハイキングコースへの入り口から
はじめの2週間ほどで何か物足りなくなってしまい、距離を長くしようかとも考えた・・・が
「いや、まてよ」、登山の練習もかねて、ザックに8kgほどの重しをいれて歩く事にした。
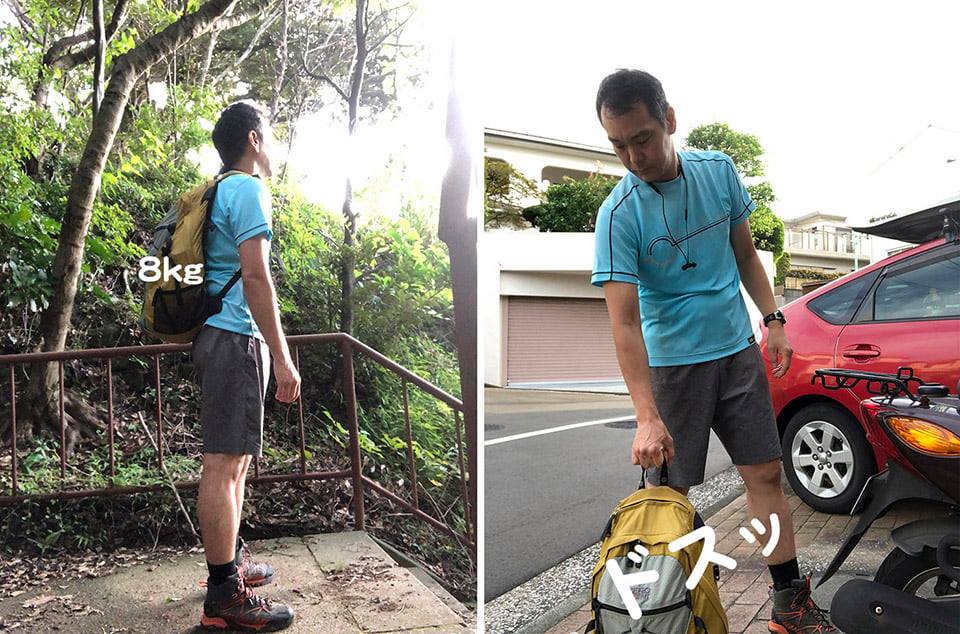
はじめのうちはこれがけっこう効きました・・・・帰ってきてザックを下ろすとまるで羽が生えたかのように身体が軽くなる!
そこでふと思い出したのがドラゴンボール
・
・
・
・
・
・
・
・
・
・
・
・
・
・
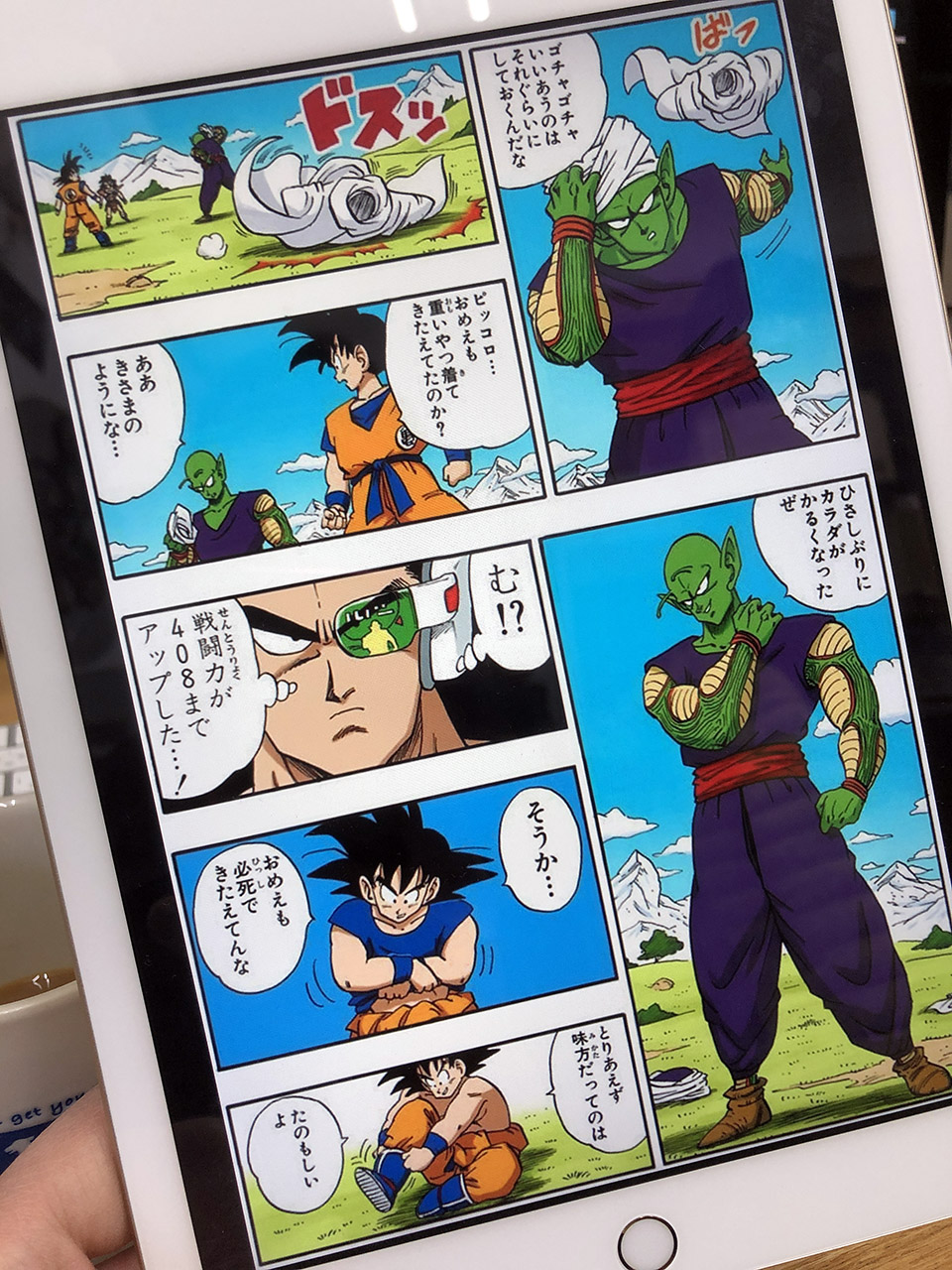
う〜ん、私の戦闘力も「100」くらいになったかな?
ブレイシング製作
当時、アコギの製作家を目指していたという事は書きましたが、お客様からお預かりした楽器や、以前に勤めていた楽器屋さんに頼んだりして、名の知れた製作家のアコギ寸法を調べまくっていた。
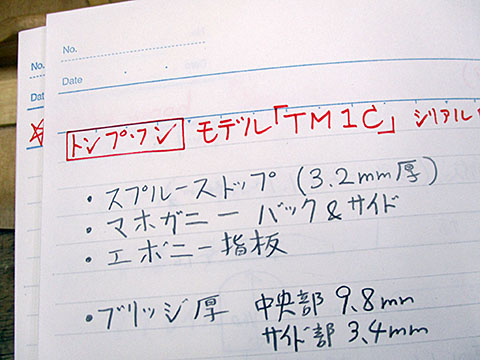
何本ものアコギを調べていくと、トップ板はたいてい薄くても2.8mm、厚くて3.2mmとかだった。面白い事に、トップ板が薄めで製作されているギターのブレイシングは、そのぶん背を高くして強度を保っている。トップ板が厚めの場合はその逆だ。
勿論、トップ板の厚みは中央付近を参考にしている。なぜなら、最終的にトップ板の外周はボイシングといって研磨し、意図的に薄くする作業があるからです。端っこの厚みは薄くなっているので参考になりません。
*量産品は均一の厚みです(おそらく)
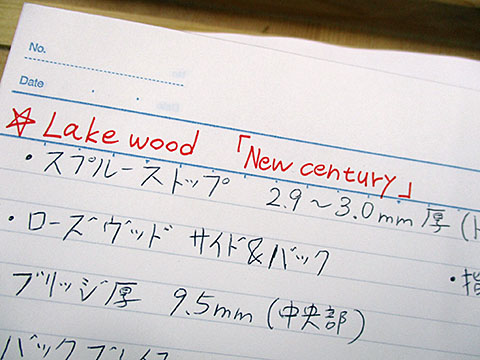
←因みにコレはプロトタイプのアコギを作った時のデータ。たしかこの時の試作品は側板や裏板も厚めで、ちょっと頑丈に作りすぎてしまい、サウンドはカッチカチだった記憶がある・・・・
これらのデータをもとに、今回製作するトップ板のブレイシング寸法を考えていきますが、忘れてはいけないのがオリジナルは「合板」という事。
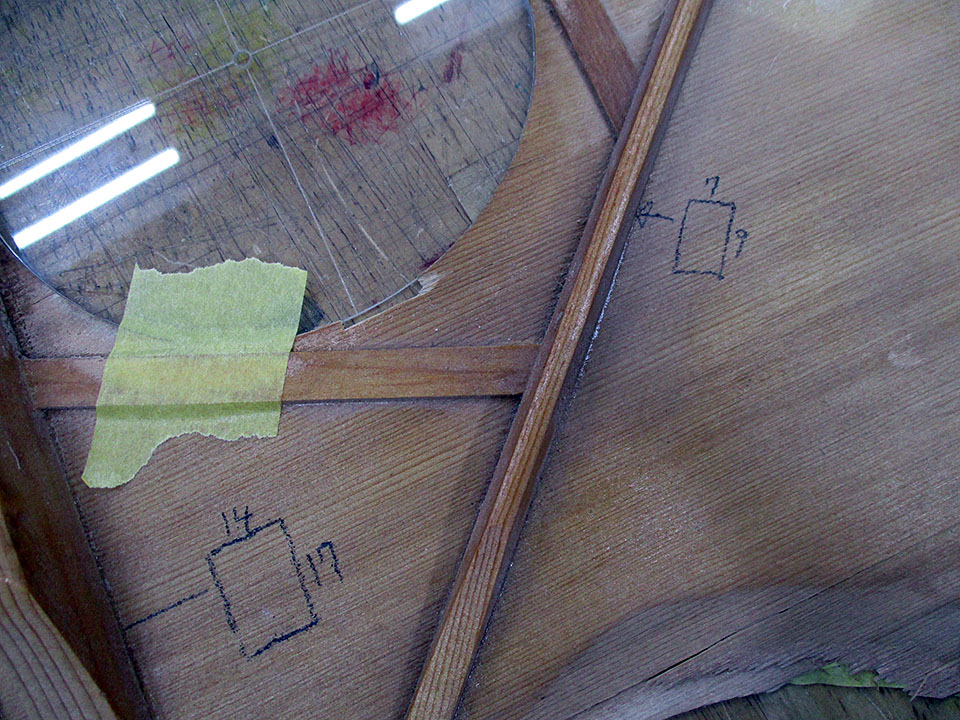
一般的に「合板」のほうが曲げや強度など強くなります。新しく作るトップ板は「単板」ですから、オリジナルどおりのブレイシング寸法では強度不足です。
因みに上画像のとおりオリジナルのXブレイシングは「幅7.0mm/高さ9mm」です。一般的なXブレイシングの寸法は「幅8.0mm/高さ15〜16.0mm」ですから、かなり細い事が分かります。YAMAHAが「合板」という事を意識してこの細い「設計/仕様」にしたのかどうか知る由はありませんが、ちょっと細すぎるのでは?と思います。
*この後、修理依頼でFGシリーズ(オールド)を何本かお預かりする機会に恵まれ、意識してブレイスの大きさを見るとほとんどがこのケースと同じくらいの大きさでした。
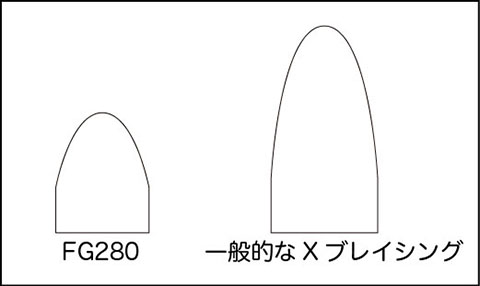
感覚的にお分かりだと思いますが、当然ながら「高さ」が高くなればそれだけ曲げる力(トップ板の上下方向)に対しては強くなります。
さて、ブレイシングを作る前に、サウンドホールの穴開けをしておきましょう。ブレイシングを接着してしまうと作業しにくいので。
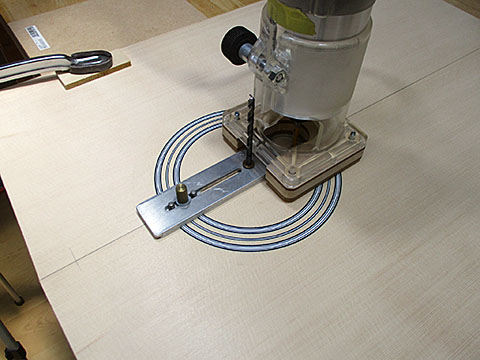
くりぬいた瞬間に抜いた材があばれないよう、両面テープで固定して、クルッ、ポン!
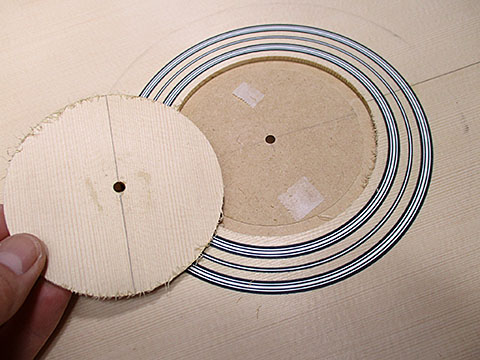
ブレイシング用のスプルース材はステュMacなどで売られていますが、木材屋などで入手する場合は木目方向に注意しましょう。
どの方向の「曲げ」に対して強度を確保したいか考えれば当然ですね。
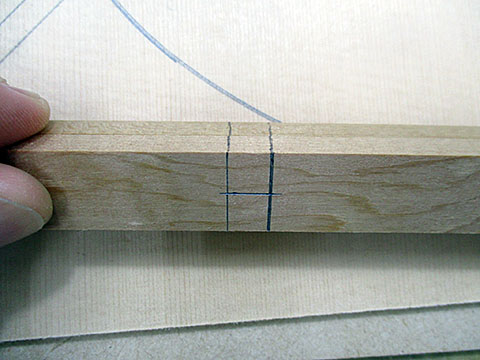
交差部は直角ですから簡単。2本まとめて半分まで切り込みをいれてあとはノミで微調整。
→→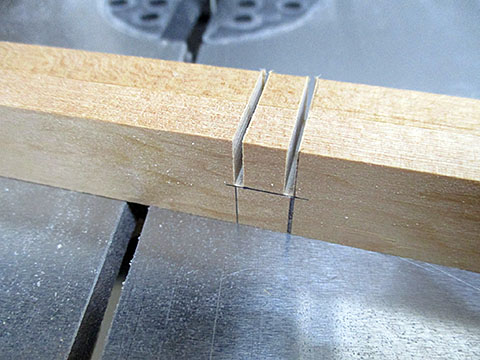
→→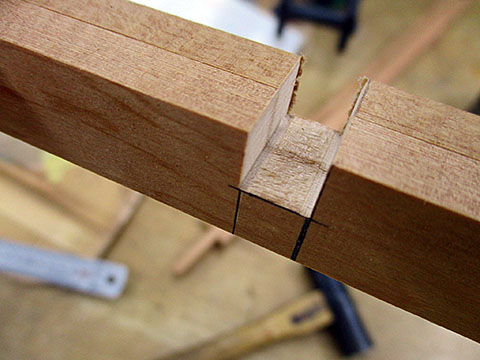
きつすぎず、ゆるすぎず、ピッタリ合わさればOK→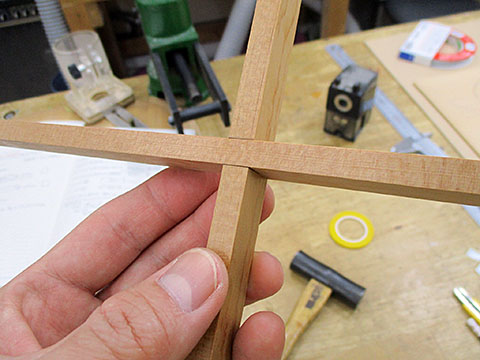
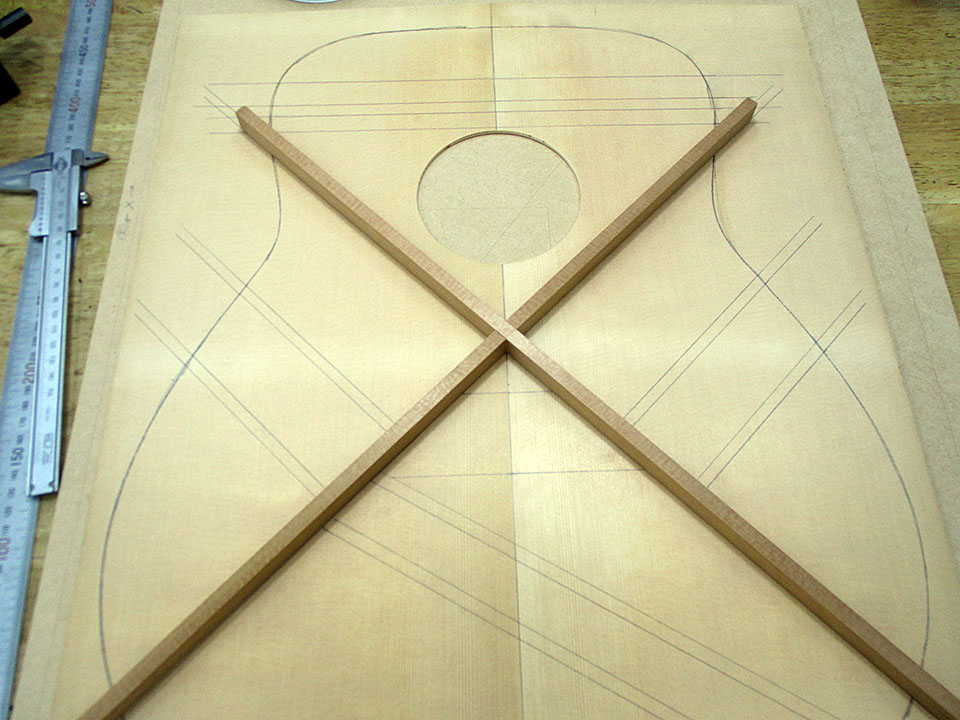
ところで知ってました? Xブレイシングとトランスバースブレイスは接着面をカーブ(曲面)にして接着します。
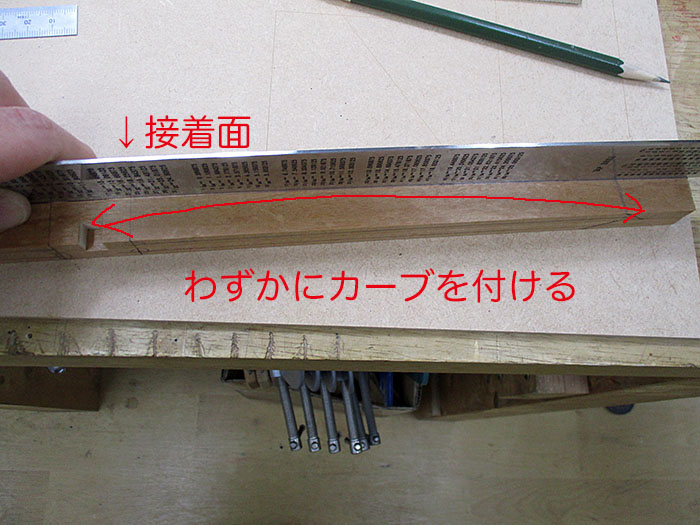
ステンレス定規などでカーブを描いたら・・・・
ベルトサンダーで削ります。交差部を中心に。
アコギの場合↓↓このように力が加わります。
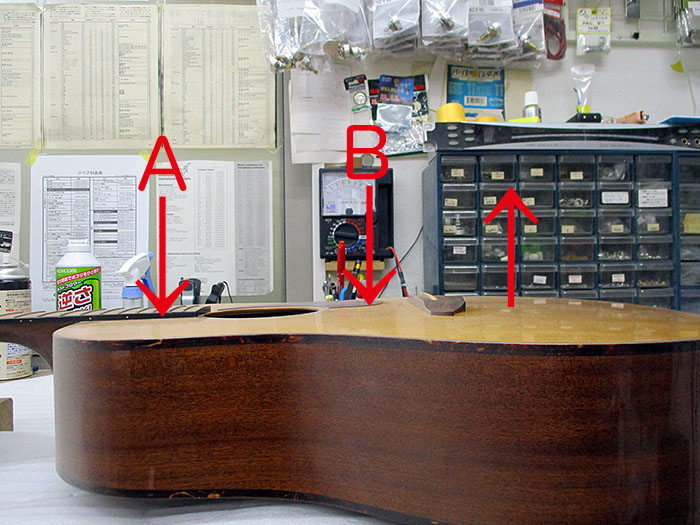
ちょうどAあたりがトランスバースブレイス、BがXブレイシングの交差部。
弦の張るとボディのA&Bにはかなりの力が加わるので、あらかじめブレイシングをカーブさせて接着する事により
その力に反発するように工夫してます。
↓カーブが付いているのが分かりますか?↓
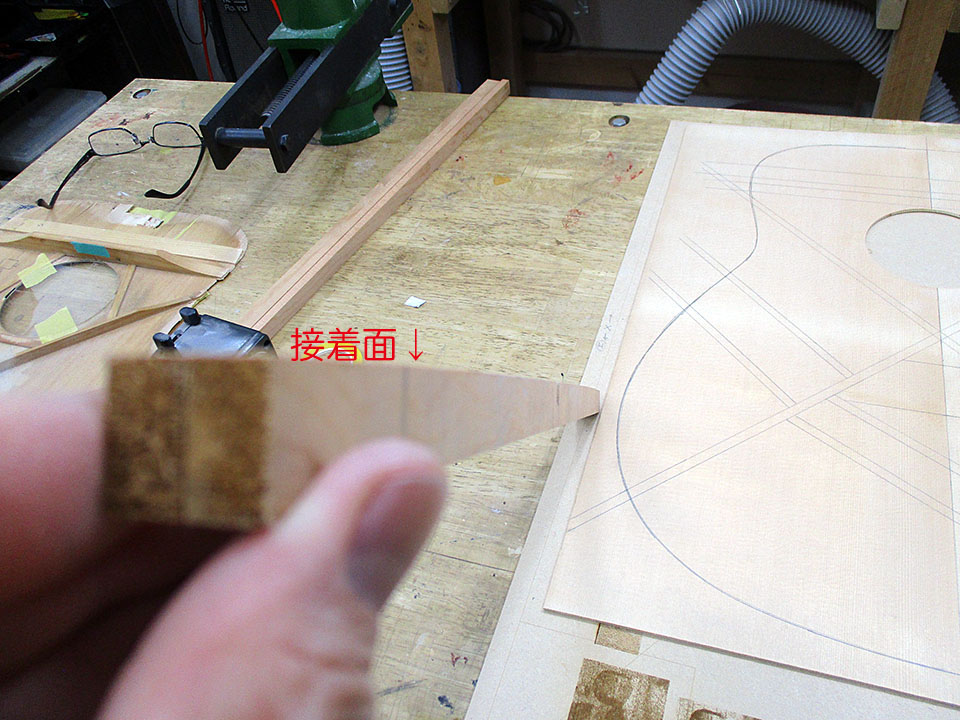
カーブを付けたら、成形。
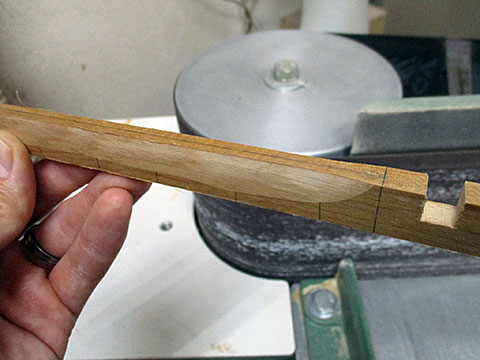
自分の好きな方法でかまいませんが、私の場合ベルトサンダーや反り台カンナなど。
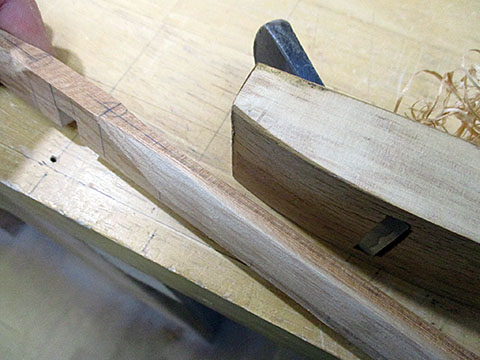
スキャロップド加工をする前に、サンドペーパーであらかた綺麗に。
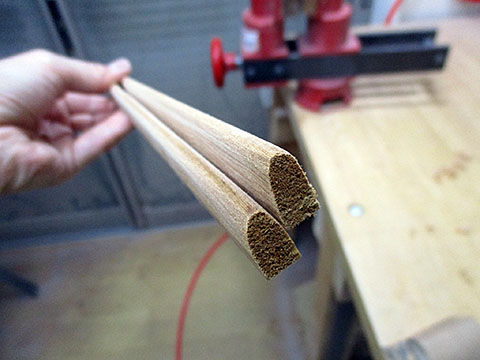
端っこは↓↓このように・・・・
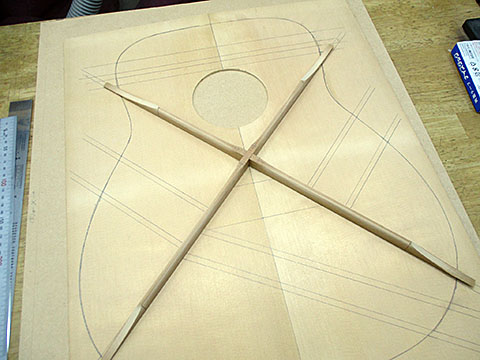
続いてトランスバースブレイシング。
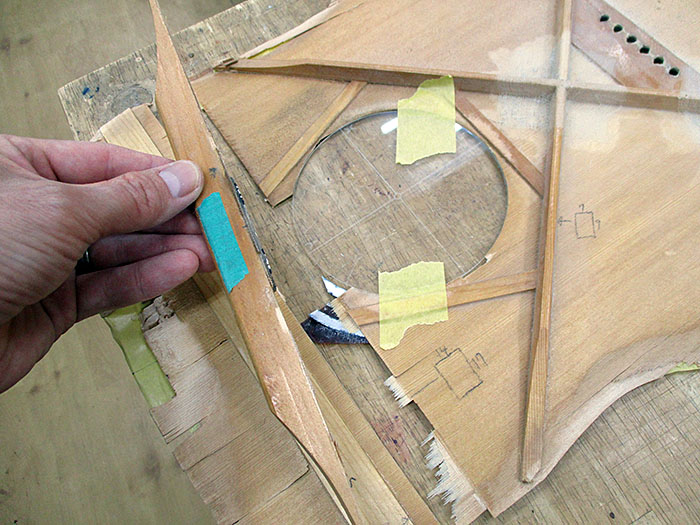
これはオリジナルのトランスバースを外して移植しました。
寸法も細すぎず普通でしたし、マスキングテープの部分にはシリアルNoも書かれていたので。
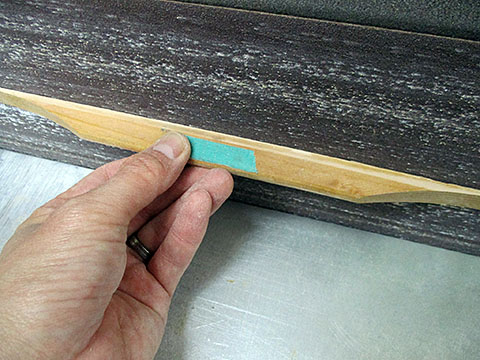
接着面などを綺麗にして準備OKです。このオリジナルの↑↑トランスバースブレイスも、接着面にはカーブが付いてました。
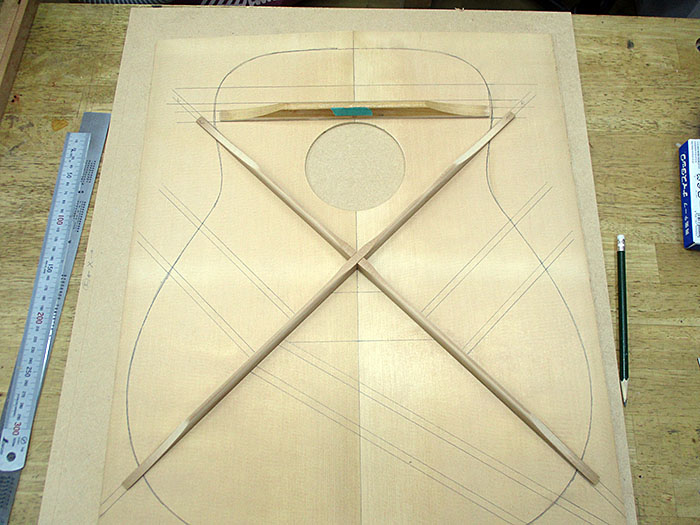
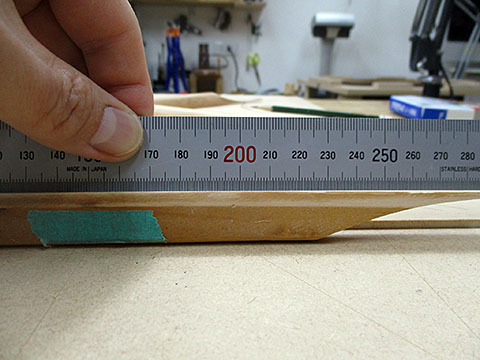
最後にスキャロップド加工します。
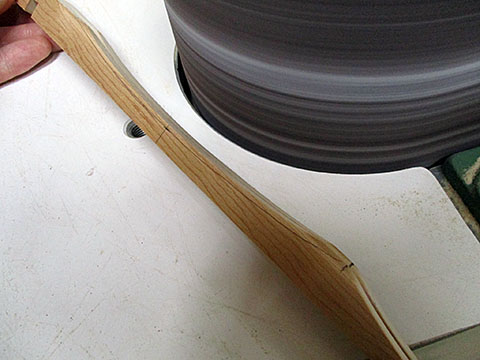
このスキャロップド加工も、接着してから最後のボイシング作業の時に行う方もいたり、様々。
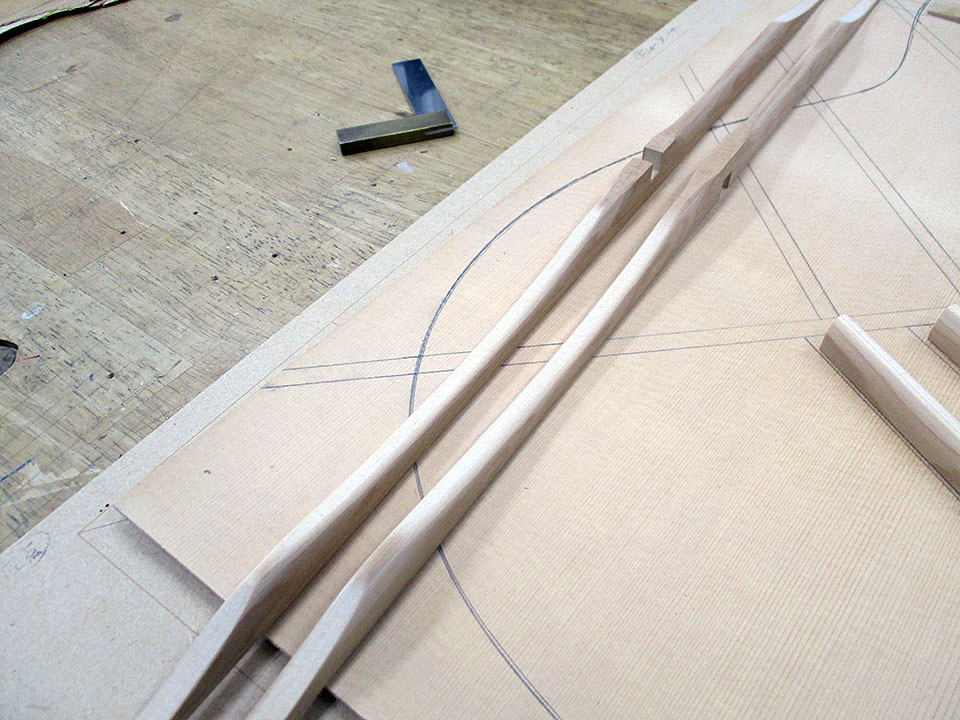
その他のブレイシングも作ります→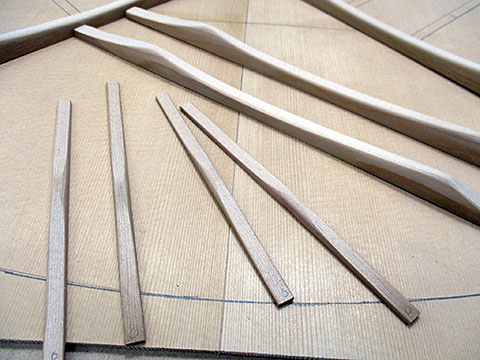
サウンドホールの内側端は↓↓このように綺麗に丸みを付けます。
→→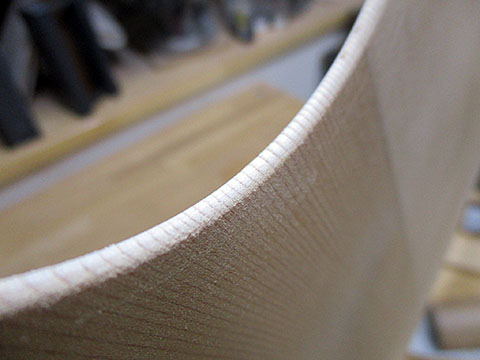
ええと、これは何だっけ。トランスバースの上に接着される薄い板。名前は無いか?
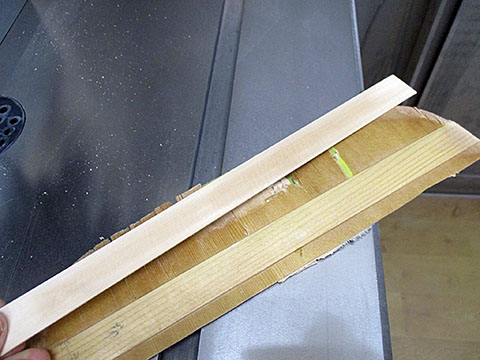
ブレイシングを接着する前に、トップ板はカットします。(カットしない製作家もいる。手順は人それぞれ)
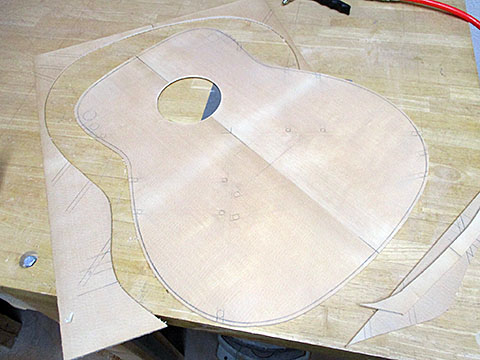
全て揃いました! *仮置き
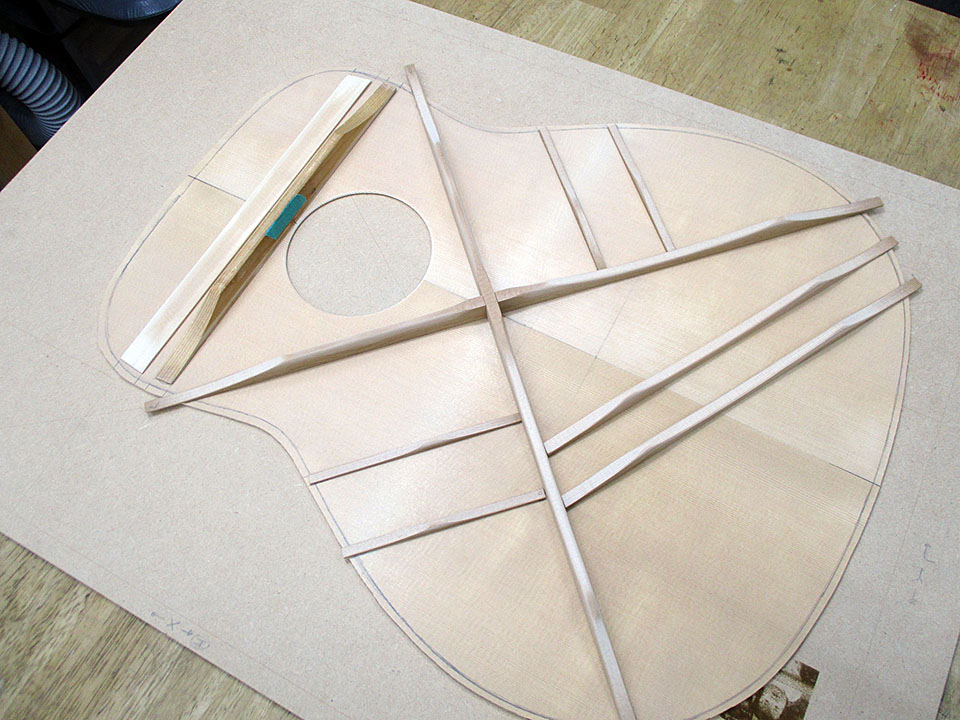
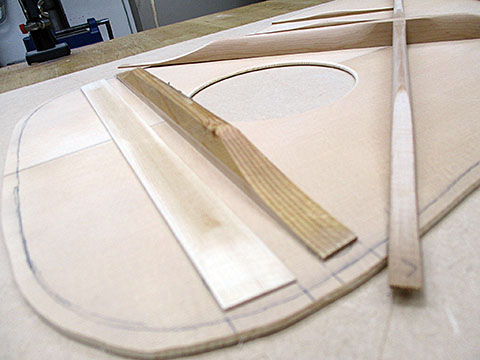
ブリッジプレートとサウンドホールの周りに接着する薄板は、ブレイシングを接着してから製作&接着します。
2021.01.01. ----5ページ目----- PAGE 1 2 3 4 5 6 7 8 9 10